Elevate Workplace Safety with Expert H2S Training
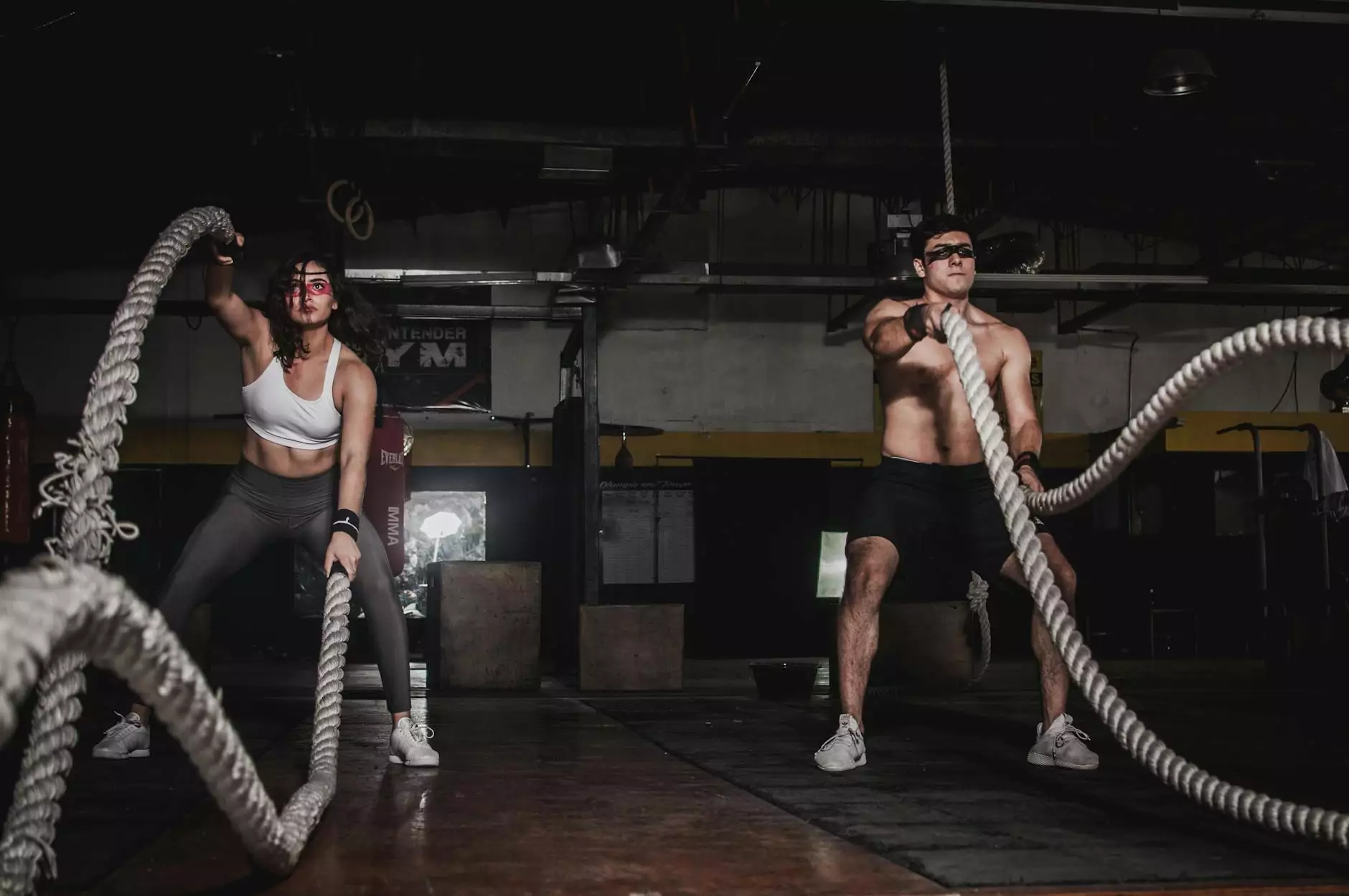
Hydrogen sulfide (H2S) is a colorless, flammable gas known for its distinctive rotten-egg odor. While its presence is often associated with oil and gas production and sewage treatment, H2S can be found in various industrial settings. Recognizing the significant dangers posed by this gas, businesses must prioritize the implementation of thorough H2S training protocols to protect their workforce. This article will delve into the importance of H2S training, outline comprehensive training techniques, and highlight how organizations can ensure safety and compliance in hazardous environments.
Understanding the Risks of Hydrogen Sulfide
Understanding the risks associated with hydrogen sulfide is crucial for any business operating in relevant industries. H2S can pose both immediate and long-term health risks. Exposure can lead to:
- Respiratory Distress: Even at low concentrations, H2S can cause irritation to the eyes, nose, and throat. Higher concentrations can lead to severe pulmonary damage.
- Nausea and Dizziness: Victims of H2S exposure may experience acute nausea, dizziness, and headaches.
- Unconsciousness: In high concentrations, H2S can lead to sudden loss of consciousness, presenting immediate dangers in the workplace.
- Death: Prolonged exposure to high concentrations can be fatal, making awareness and training absolutely essential.
Why H2S Training is Essential for Your Workforce
The importance of H2S training cannot be overstated. Here are several compelling reasons why businesses must implement consistent and thorough training programs:
- Regulatory Compliance: Various safety regulations require proper training on hazardous materials, including H2S. Failure to comply can result in hefty fines and legal ramifications.
- Workplace Safety: Training significantly reduces the number of incidents related to H2S exposure, ensuring the safety of employees and creating a culture of safety within the organization.
- Emergency Preparedness: Proper training ensures employees are equipped to handle emergencies, including leaks or unexpected exposure, which is critical for minimizing harm.
- Boosting Employee Morale: When workers feel safe and prepared, their morale increases, contributing to higher productivity and job satisfaction.
Comprehensive H2S Training Programs
To effectively equip employees with the necessary knowledge and skills, businesses should consider implementing a comprehensive H2S training program. Here’s how a well-structured program can be organized:
1. Classroom-Based Training
Classroom-based training is a fundamental component of H2S education. It offers an interactive environment where trainers can introduce:
- The properties and behaviors of hydrogen sulfide.
- The physiological effects of H2S exposure.
- Regulatory standards associated with hydrogen sulfide safety.
- Safety data sheets and understanding risk assessments.
2. Hands-On Training
Having theoretical knowledge is essential, but practical application is critical. Hands-on training should include:
- Use of personal protective equipment (PPE).
- Utilizing detection and monitoring equipment.
- Emergency response practices, including evacuation procedures.
- Simulations of potential H2S exposure scenarios.
3. Continuous Learning and Refresher Courses
Safety training should not be a one-time event. Regular refresher courses can help keep safety top of mind and include:
- Updated safety regulations and best practices.
- Reviews of incident case studies and lessons learned.
- Adaptations to emergency procedures as new technology or equipment is introduced.
Choosing the Right H2S Training Provider
Not all training providers are the same; choosing the right one is vital for ensuring quality education and effective implementation. Consider these factors:
- Experience and Credentials: Look for a provider with a strong track record in H2S training. They should have certified instructors with industry experience.
- Customized Training Programs: Ensure the program can be tailored to meet the specific needs of your organization and employees, considering industry standards and operational requirements.
- Hands-On Training Opportunities: Verify that they offer practical, hands-on training sessions as part of their curriculum.
- Positive Reviews and Referrals: Look for online reviews and testimonials from past clients to gauge the effectiveness and satisfaction levels of their training.
The Role of Technology in H2S Training
Advancements in technology have significantly enhanced training methods. Using technology in H2S training can include:
- Virtual Reality (VR) Training: This immersive experience allows employees to face realistic scenarios without exposure to real risks, making it an excellent tool for training.
- Online Training Modules: Many organizations now offer digital courses that employees can take at their own pace, making training more accessible.
- Simulation Software: Software that simulates H2S environments allows trainees to engage in decision-making and crisis management without being in real situations.
Regulatory Requirements for H2S Safety
Incorporating H2S training is not just about safety; it is also about compliance with laws and regulations. Several regulatory bodies, including OSHA (Occupational Safety and Health Administration) and NIOSH (National Institute for Occupational Safety and Health), set strict guidelines regarding hazardous materials. Key regulations to consider include:
- OSHA 1910.134: This regulation outlines the need for a respiratory protection program for any worker exposed to H2S.
- ANSI Z390.1: The American National Standards Institute provides guidelines for training employees who work in environments with potential H2S exposure.
- Local Regulations: Different states or regions may have additional regulations regarding H2S safety training; understanding these is crucial for compliance.
Creating a Culture of Safety
Developing a strong culture of safety goes beyond training; it requires continuous reinforcement of safety as a core value. Here are ways to establish this culture within your organization:
- Encourage Open Communication: Create an environment where employees feel comfortable discussing safety concerns without fear of punishment.
- Regular Safety Meetings: Hold frequent safety meetings to discuss protocols, share knowledge, and highlight recent incidents or near misses.
- Recognize and Reward Safe Behavior: Positive reinforcement can motivate employees to take safety seriously and engage in safe practices.
- Involve Employees in Safety Programs: Engage your workforce in the development and evolution of safety protocols to ensure they feel invested in the process.
Conclusion: Investing in H2S Training is Investing in Safety
In conclusion, H2S training is a critical investment for any organization that operates in environments where hydrogen sulfide is present. By prioritizing education, hands-on experience, and compliance with regulations, businesses can enhance safety, ensure legal compliance, and significantly reduce the risks associated with H2S exposure. As you consider your approach to H2S training, remember that the well-being of your employees and the longevity of your business depends on your commitment to fostering a safe working environment. Empower your team with knowledge, equip them with skills, and create a culture of safety that will drive your organization forward.