The Power of **Low Pressure Casting** in Modern Business
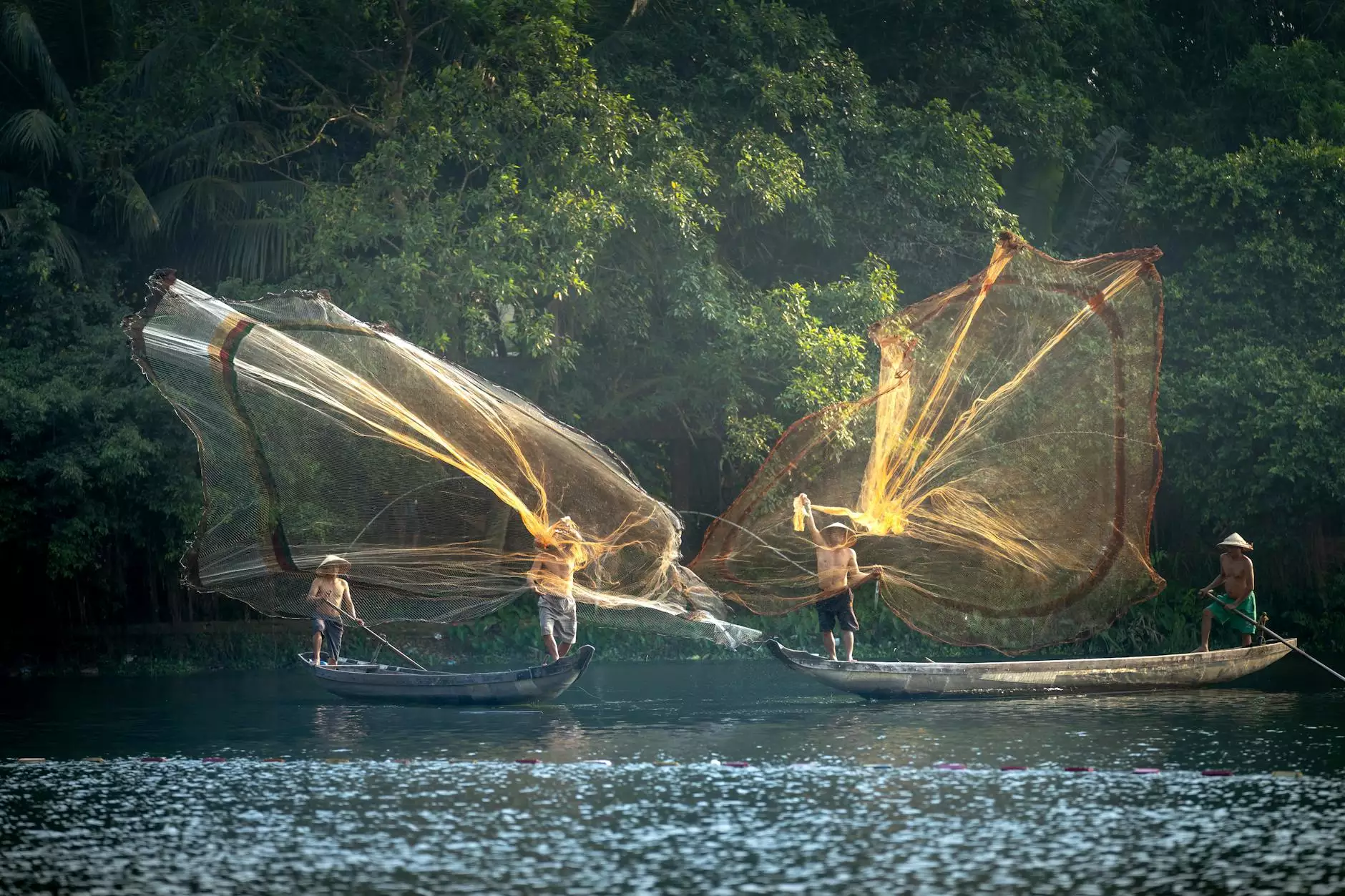
In an era where innovation drives competition and market success, low pressure casting stands out as a revolutionary manufacturing technique that is redefining how products are designed and created. This article delves into the various aspects of low pressure casting, how it integrates with art supplies, product design, and 3D printing aspects of arti90.com, and why this method should be at the forefront of contemporary business strategies.
Understanding Low Pressure Casting
Low pressure casting, also known as low pressure die casting, is a sophisticated process that utilizes controlled pressure to fill a mold with molten materials, typically metals, in a way that minimizes defects and improves finish quality. Unlike traditional high-pressure methods, low pressure casting operates at relatively low pressures, which allows for precise control over the material flow and significantly reduces turbulence and gas entrapment in the castings.
Advantages of Low Pressure Casting
- Enhanced Quality: The controlled environment in which low pressure casting operates leads to fewer defects and improved surface finish.
- Design Flexibility: This method permits the casting of complex shapes, which is ideal for innovative product design.
- Material Efficiency: Reduced waste materials compared to traditional methods.
- Cost-Effectiveness: Lower energy consumption and reduced scrap rates lead to substantial cost savings in large-scale productions.
- Better Mechanical Properties: Products manufactured through low pressure casting often exhibit superior strength and durability.
How Low Pressure Casting Revolutionizes Product Design
In product design, the concept of creating unique and functional products is paramount. Low pressure casting enhances this by allowing designers to create components with intricate geometries that would be impossible or cost-prohibitive with other casting methods. For instance, in the automotive industry, low pressure casting is used to make lightweight yet strong engine components that are essential for fuel efficiency.
Moreover, the possibility of using a wide range of materials, including aluminum and magnesium alloys, further broadens the horizons for product designers. Notably, industries focused on art supplies also benefit, as manufacturers can create bespoke tools and materials tailored to the needs of artists, improving their creative process.
Applications of Low Pressure Casting in Various Industries
The utility of low pressure casting spans multiple industries, showcasing its versatility and effectiveness. Here are a few notable applications:
1. Automotive Industry
In automotive manufacturing, low pressure casting is used extensively to create high-performance components that require precise specifications and durability. Key components like transmission housings, engine blocks, and structural parts benefit from this innovative casting technique.
2. Aerospace Sector
In aerospace, where weight and strength are crucial, low pressure casting facilitates the production of lightweight components that can withstand extreme conditions, thereby enhancing performance and safety.
3. Art Supplies Manufacturing
For art supply manufacturers, low pressure casting allows for the production of intricate mold designs that can yield unique tools. With a focus on creativity and aesthetics, this technique ensures high-quality finishes that meet the precise expectations of artists and designers.
4. 3D Printing Synergy
Integrating low pressure casting with 3D printing opens up new avenues for innovation. Designers can first create prototypes using 3D printing, allowing for easy modifications before casting the final product in a low pressure mold. This synergy not only saves time but also encourages experimentation, reducing the risk involved in the prototyping stage.
Technological Advancements Supporting Low Pressure Casting
With advancements in technology, low pressure casting has evolved significantly. The introduction of computer-aided design (CAD) and computer-aided manufacturing (CAM) technologies has refined the casting process:
- 3D Modeling: Modern design software allows for precise modeling of the components, ensuring that the mold can be designed with exact specifications.
- Simulation Software: Engineers can simulate the casting process, predicting potential issues and optimizing designs before actual production.
- Automation: Automated systems improve consistency and reduce human error in the casting process.
Impact of Low Pressure Casting on Sustainability
As businesses increasingly focus on environmental responsibility, low pressure casting emerges as a more sustainable manufacturing option. This method produces significantly less material waste when compared to traditional casting techniques. By minimizing defects and reducing energy consumption, companies can create products with a lower carbon footprint. Moreover, the potential to use recycled materials further aligns with global sustainability goals.
Case Studies: Success Through Low Pressure Casting
Case Study 1: Automotive Component Production
A leading automotive manufacturer implemented low pressure casting in the production of its engine components. By switching from high-pressure die casting to low pressure, the company reported a 30% increase in production efficiency and a 20% reduction in material costs. The improved finish quality also led to enhanced customer satisfaction and a reduction in post-production processes.
Case Study 2: Innovative Art Supplies
An art supplies company sought to create a new line of paintbrushes featuring unique ergonomic designs. Utilizing low pressure casting, they were able to replicate complex shapes with a high level of detail. The result was a collection of high-quality paintbrushes that gained positive reviews from professional artists, ultimately leading to a 50% increase in sales within one year.
Challenges and Considerations in Low Pressure Casting
While the benefits of low pressure casting are numerous, businesses must also consider certain challenges:
- Initial Investment: Setting up a low pressure casting setup can require a significant capital investment for equipment and technology.
- Training Requirements: Employees need specialized training to handle the technology and processes involved effectively.
- Material Selection: Not all materials are suitable for low pressure casting; businesses must carefully choose which materials to use based on their specific requirements.
The Future of Low Pressure Casting in Business
The future of low pressure casting looks promising, with advancements likely to enhance its efficiency and effectiveness. As industries continue to innovate and demand for unique, high-quality products rises, techniques like low pressure casting will be essential. Furthermore, as sustainable practices become integral to business models, the eco-friendly nature of low pressure casting positions it as a preferred method for future manufacturing.
Conclusion
In conclusion, low pressure casting is more than just a manufacturing method; it is a transformative process that propels businesses forward in the competitive landscape. Its advantages in improving product quality, enhancing sustainability, and fostering innovative designs make it a crucial component for industries ranging from automotive to art supplies. By embracing low pressure casting, businesses can not only meet current market demands but also set the stage for future advancements, solidifying their positions in their respective fields.
For businesses aiming to innovate and lead, implementing low pressure casting is a decisive step towards optimizing manufacturing processes and achieving greater operational efficiency. As we look ahead, let us recognize the profound impact of this technology on shaping the future of various industries.