The Importance of Injection Mold Tools in Metal Fabrication
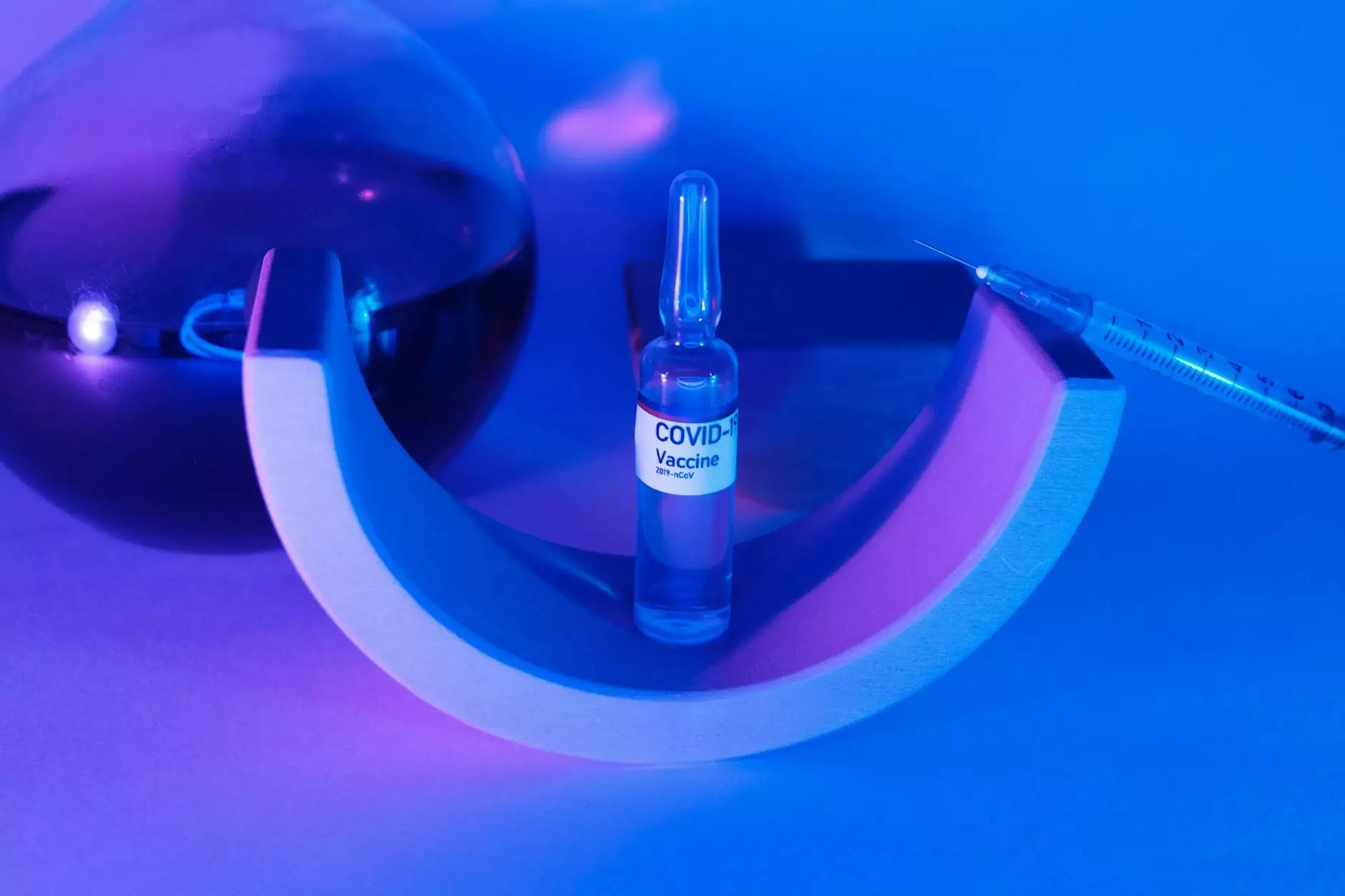
In the rapidly evolving landscape of manufacturing, the injection mold tool holds a pivotal role, particularly within the metal fabrication industry. Utilizing advanced technology and innovative techniques, businesses are increasingly reliant on these tools to enhance production efficiency, improve product quality, and reduce costs. This article delves deep into the world of injection mold tools, exploring their significance, functionality, applications, and the future of metal fabrication.
Understanding Injection Mold Tools
Injection mold tools are specialized machinery designed to produce parts by injecting molten material into a mold. This process is essential not only in plastic fabrication but also in metal working, where it provides unmatched precision and versatility. The core components of an injection mold tool include:
- Mold Base: This holds the mold cavity and core components in place.
- Cavity: The hollow part of the mold that shapes the final product.
- Core: The part that creates the internal features of the molded item.
- Injection System: The mechanism that injects the molten material into the mold.
- Ejection System: This facilitates the removal of the finished part from the mold.
Benefits of Utilizing Injection Mold Tools
The injection mold tool process brings numerous benefits to businesses engaged in metal fabrication:
1. Increased Production Efficiency
Injection molding is capable of producing large quantities of parts with minimal downtime. This efficiency translates into increased productivity, allowing manufacturers to meet demanding production schedules.
2. High Precision and Consistency
With the ability to produce parts with tolerances of ±0.001 inches, injection mold tools ensure a high level of accuracy and consistency across all manufactured products, resulting in reduced waste and increased customer satisfaction.
3. Cost-Effective Manufacturing
While the initial setup cost for injection mold tools can be significant, the long-term savings achieved through reduced labor costs and material waste make it worthwhile. Moreover, the ability to use recyclable materials further minimizes expenses.
4. Design Flexibility
Injection molding allows for intricate designs and complex part geometries that would be challenging or impossible to achieve with traditional metalworking techniques. This flexibility opens new avenues for product development and innovation.
Applications of Injection Mold Tools in Metal Fabrication
Injection mold tools find application across various sectors within metal fabrication, including:
- Aerospace: Manufacturing lightweight, high-strength components that meet stringent safety standards.
- Automotive: Producing precise parts that contribute to vehicle efficiency and performance.
- Consumer Electronics: Creating complex housings and structural components in gadgets and devices.
- Medical Devices: Ensuring the production of reliable, accurate components crucial for health applications.
Challenges in Injection Molding
Despite its advantages, the use of injection mold tools is not without challenges. These may include:
1. High Initial Costs
As previously mentioned, the initial investment for high-quality injection molds can be substantial. However, this should be viewed as a strategic investment that provides long-term benefits.
2. Design Constraints
The complexity of the mold design can affect manufacturability and may limit geometric freedom. This necessitates experienced engineers to allow for both creativity and practicality in design.
3. Maintenance Requirements
Frequent maintenance is crucial to ensure that injection mold tools function optimally. Neglecting maintenance can lead to production delays and increased costs.
Choosing the Right Injection Mold Tool Manufacturer
Selecting a reputable manufacturer for injection mold tools is critical for achieving the best outcomes in metal fabrication. Here are some tips for choosing the right partner:
1. Experience and Expertise
Look for manufacturers with extensive experience in the metal fabrication industry, as they will have a better understanding of the complexities and requirements involved in injection molding.
2. Technological Capabilities
Ensure that the manufacturer employs the latest technologies and adheres to industry standards. Advanced equipment and software can greatly enhance production precision.
3. Customization Options
Every project has unique needs. Choose a manufacturer that offers customized solutions to meet specific requirements and challenges.
4. Robust Quality Assurance
Partnering with a manufacturer that has a stringent quality assurance process can significantly reduce the risks of defects and ensure a smooth production flow.
The Future of Injection Mold Tools in Metal Fabrication
The future of injection mold tools appears bright, bolstered by technological advancements and a growing demand for high-quality manufacturing processes. Technologies such as 3D printing and computer-aided design (CAD) are increasingly being integrated into injection molding processes to optimize efficiencies and enhance capabilities.
1. Automation and Smart Manufacturing
With the rise of Industry 4.0, integrating robotics and automated systems into the injection molding process will further enhance production rates and precision, leading to smarter, more efficient manufacturing practices.
2. Eco-Friendly Materials
Sustainability is becoming a critical focus for manufacturers. The incorporation of biodegradable materials and recycling initiatives within the injection molding process will play an essential role in shaping the future of metal fabrication.
Conclusion
In conclusion, the injection mold tool is a cornerstone of efficient, high-quality manufacturing in the metal fabrication industry. By understanding the benefits, applications, and future of these tools, companies can leverage them for competitive advantage. The right investment in injection mold technology not only enhances production efficiency but also drives innovation and sustainability within the industry. For businesses looking to stay at the forefront of technology and quality, investing in advanced injection mold tools is not just an option—it's essential.
For more information about metal fabrication and how injection mold tools can benefit your business, visit deepmould.net.