Delving Deep into Injection Moulding Manufacturing
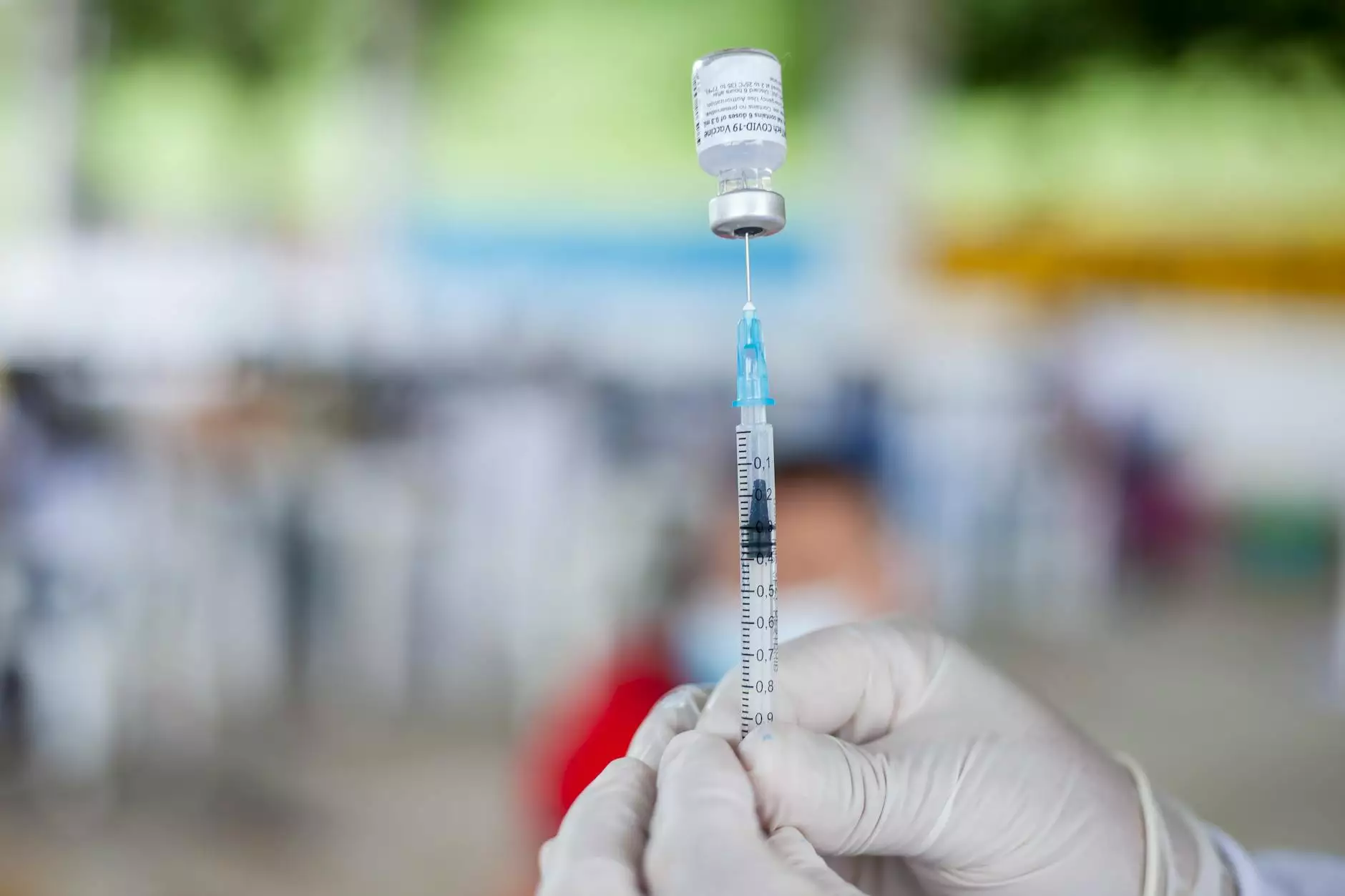
Injection moulding manufacturing is a pivotal technique in the production of a wide array of plastic components that play essential roles across various industries. From consumer goods to automotive parts, this process spearheads innovation, efficiency, and scalability in manufacturing. In this extensive article, we'll explore the nuances of injection moulding, its advantages, processes, common applications, and the future trends shaping its landscape.
What is Injection Moulding Manufacturing?
Injection moulding manufacturing refers to a process where molten material, usually plastic, is injected into a mould to create items of a specific shape and design. Upon cooling, these items solidify, taking the form of the mould. This manufacturing technique is favored due to its ability to produce high volumes of identical pieces with remarkable precision.
The Injection Moulding Process Explained
1. Material Selection
The choice of material is a crucial initial step in the injection moulding manufacturing process. Commonly used materials include:
- Thermoplastics: These plastics can be reheated and reshaped numerous times, making them versatile for applications.
- Thermosetting Plastics: Unlike thermoplastics, these materials undergo a chemical change when heated, resulting in a hard and inflexible structure.
- Elastomers: These materials offer exceptional flex and resilience, useful in applications requiring flexibility.
2. Mould Design
The mould design is integral to producing high-quality parts. Engineers utilize software for 3D modelling to ensure the design meets all functional and aesthetic requirements. Factors considered in mould design include:
- Draft Angles: This aids in the easy removal of the part from the mould.
- Gate Design: The point where the molten material enters the mould affects the flow and finish of the part.
- Cooling Channels: These channels ensure even cooling of the part to prevent warping.
3. Injection
During this stage, the selected material is heated until it reaches a molten state and is then injected into the mould under high pressure. The pressure ensures that the material fills every cavity of the mould, allowing for intricate designs. This phase must be executed rapidly and precisely to prevent premature solidification.
4. Cooling and Solidification
After the material is injected, it needs to cool down to solidify. Cooling times can vary significantly based on the part's size and complexity as well as the material used. A properly designed cooling system can dramatically reduce production cycles and increase efficiency.
5. Ejection
Once the part has solidified, it is crucial to eject it from the mould without any damage. This typically involves mechanisms like ejector pins, air blast, or a combination of both. The efficacy of this process directly affects the quality of the finished product.
Benefits of Injection Moulding Manufacturing
1. High Efficiency
The injection moulding manufacturing process is notably fast, allowing for the mass production of components in short timeframes. Once the mould is made, thousands of identical parts can be produced in a day, significantly reducing manufacturing time and costs.
2. Precision and Consistency
Injection moulding excels at creating parts with high levels of precision. The closed mould system ensures that each part produced is almost identical, which is essential for industries that require stringent quality control.
3. Cost-Effective for Large Volumes
While the initial cost of mould creation can be substantial, injection moulding manufacturing becomes more cost-effective as production volumes increase. The per-unit cost decreases significantly with higher volume runs.
4. Material Versatility
This process allows for a diverse range of materials to be used, making it suitable for nearly any application. Additives and modifications can be introduced to enhance performance characteristics like UV resistance, strength, or flexibility.
5. Minimal Waste
The process is also known for producing minimal waste compared to other manufacturing methods, as excess materials can often be recycled and reused, further enhancing its sustainability.
Applications of Injection Moulding Manufacturing
The versatility of injection moulding makes it applicable across various sectors. Here are some of the key industries leveraging this technology:
1. Automotive Industry
In the automotive sector, injection moulding is employed to produce components such as dashboards, bumpers, and internal fixtures. These elements require not only durability but also a high degree of aesthetics, making injection moulding ideal due to its precision.
2. Consumer Products
The production of everyday consumer goods, such as containers, toys, and appliances, utilizes injection moulding extensively. The ability to quickly produce custom shapes makes it a favorite in this sector.
3. Medical Devices
Medical devices demand stringent compliance with regulatory standards. Injection moulding allows the production of precise and sterile components, such as syringes and surgical tools, tailored to meet specific requirements.
4. Electronics
In electronics, injection moulding is used for creating enclosures, connectors, and other components that require durable and lightweight materials. The precision of the moulding process is beneficial for housing sensitive electronic instruments.
5. Packaging
This manufacturing technique is widely used in producing plastic packaging solutions, including bottles, containers, and lids. The customizability of moulds enables the production of a variety of shapes and sizes to meet market demand.
Future Trends in Injection Moulding Manufacturing
As technology advances, the landscape of injection moulding manufacturing is also evolving. Here are some future trends to watch:
1. Automation and Robotics
Incorporating automation and robotics into the injection moulding process can lead to increased efficiency and reduced human error. Automated systems can handle repetitive tasks, freeing up skilled labour for more complex processes.
2. Sustainability Practices
As industries place more emphasis on sustainability, injecting recycled materials and reducing waste are becoming priorities. There is a growing trend to improve recyclability and reduce the carbon footprint of the manufacturing process.
3. Advanced Materials
The development of new materials, particularly those with enhanced properties such as bio-based plastics and composites, is paving the way for broader applications of injection moulding. These materials can offer superior performance and environmentally friendly solutions.
4. Customisation
With advancements in digital technology, customisation is becoming increasingly accessible. Manufacturers can now produce tailored solutions on demand, responding quickly to market needs and trends.
5. Smart Manufacturing
Integration of IoT (Internet of Things) in manufacturing allows for real-time monitoring and optimization of production processes. Implementing smart moulding machines can lead to better quality control and predictive maintenance.
Conclusion
Injection moulding manufacturing stands as a critical pillar in modern industrial production, driving innovation, efficiency, and versatility. As we explore its processes, benefits, and applications, it's clear that this technology will continue to transform various industries for years to come. Staying informed about the latest trends and practices will not only assist manufacturers in remaining competitive but also in contributing to a more sustainable future. Explore more about injection moulding manufacturing at DeepMould.net, your trusted resource for all things related to advanced manufacturing technologies.